Since the promulgation of the "Cleaner Production Promotion Law of the People's Republic of China", our metal container packaging industry has to implement cleaner production in accordance with the law, improve the utilization of resources, and reduce and avoid the problems arising from pollution. This has become a grim reality for companies seeking development.
The exhaust emissions from paint drying rooms in the barrel industry are obvious. Installation of exhaust gas purification and environmental protection equipment is a relatively good solution, but because it consumes more energy (oil, liquefied petroleum gas, etc.), the reasons for increasing the operating costs of drying rooms have caused many companies to have various concerns and opinions. For this reason, I would like to introduce to you the relevant information and data on the installation of exhaust gas purification and environmental protection equipment at home and abroad in recent years. The exhaust gas purification and environmental protection equipment that can realize the “double effect of environmental protection and energy saving†is the ideal environmental protection equipment.
First, the types and principles of exhaust gas purification and environmental protection equipment are introduced:
1. Absorption purification method: It is a method that uses the different solubility of each mixed component in the exhaust gas in the selected absorbent or chemical reaction to separate the harmful gas from the exhaust gas. Used in the printing industry, it has been abandoned due to its low purification efficiency and secondary pollution.
2. Adsorption purification method: The use of porous solids (adsorbents) to accumulate harmful substances in the exhaust gas or concentrate on the surface for separation purposes. However, since the adsorbent (such as activated carbon) will gradually fail during use, it must be replaced on a regular basis, and it will also produce secondary pollution, so it is appropriate to adopt it as an expedient measure.
3. Combustion method: The combustion method for treating exhaust gas includes flame combustion (direct combustion), thermal combustion, and catalytic combustion. Due to the low concentration of exhaust gas emitted from the paint drying room, the conditions for burning and purifying itself are not available. Therefore, the latter two methods of combustion are introduced.
(1) Thermal combustion (also known as incineration):
It is based on the heat generated by the combustion of the auxiliary fuel (burner) to increase the temperature of the exhaust gas. The components of the hydrocarbons in the exhaust gas are oxidized and converted to harmless carbon dioxide and water vapor (the smoke discharged from the chimney is smokeless and tasteless). To achieve the desired purification effect. In order to achieve this purification goal, the thermal combustion in the environment-friendly furnace body must reach the "three T" condition: the furnace reaction temperature (Temperature) is about 760°C, and the exhaust gas residence time (Time) at this temperature should be sufficient, and the exhaust gas should be The oxygen mixing (turbulence) should be sufficient to fully purify the exhaust gas.
(2) Catalytic combustion method:
It is the use of catalysts in the combustion of exhaust gas to accelerate the reaction rate of exhaust gas decomposition. It requires only about 350°C to purify the exhaust gas, which is more economical than incineration. However, the composition of the catalyst (there are three parts: active component, co-catalyst, body) and the arrangement of the catalytic bed are crucial. In the furnace design is more rigorous. However, regardless of the type of catalyst in the exhaust gas purification process, its activity is gradually reduced over time, the final catalyst failure, to replace the catalyst in order to purify the exhaust gas. Therefore, the catalytic combustion method has a problem of service life.
(3) Comparison and common points of incineration and catalytic combustion:
Incineration method: burning a hundred, is the most thorough way to clean up the exhaust gas. However, purifying exhaust gas at around 760°C consumes high energy. Heat must be recycled for practical value.
Catalytic combustion method: The exhaust gas purification temperature through the catalytic bed is only about 350°C, which is lower than the incineration method. However, due to the problem of service life of the catalyst and the actual problem of heat recovery and utilization, there are many factors of change in the actual operation of the environmental protection furnace.
The two points in common are: fully utilize the heat emitted by the exhaust gas during the oxidation and decomposition to provide the temperature requirements of the combustion chamber or the catalyst chamber. Therefore, the large exhaust gas concentration is beneficial to save energy consumption.
Second, KIC environmental protection furnace features:
After the waste gas is collected, it is pumped into the environmental protection furnace and the exhaust gas purification process is performed according to the following procedures: indirect preheating → combustion heating (primary purification) → catalytic reaction (secondary purification) → heat is fed into the drying room for production use.
The treatment method of the secondary purification exhaust gas combines the principles of the incineration method and the catalytic method, achieving the dual effects of environmental protection and energy saving. The energy consumption is lower than the incineration method, and the catalyst life is longer than the catalytic method. The best effect of waste heat utilization is to stop the use of two burners in the original paint drying room. The heat recovery of the environmental protection furnace can guarantee the production use and does not affect the product quality.
Third, KIC environmental protection furnace acceptance standards
1. The purifying effect of exhaust gas is to reach the environmental protection standard stipulated by GB16297-1996 under the circumstance of no smoke and odorless.
2. The heat recovery of exhaust gas purification and environmental protection equipment can be used for production and use (the original oven burner is stopped for use) to achieve energy-saving effect.
3. Does not affect the original paint drying room temperature control accuracy.
4. Does not affect product quality.
Fourth, KIC environmental furnace application data
The environmental protection furnace has been used in printing iron, printing, and barrel making industries. The data processing is:
1 Printed iron: Under the environmental protection requirements, the remaining heat recovery reaches 700,000 kcal/hour of heat energy. The total energy consumption of the original paint drying room and Indian iron drying room is about 650,000-700,000 kcal/hour. Therefore, under the condition of continuously producing full-baked rooms, waste heat can be used for production in two drying rooms, ie, one for two. In fact, due to changes in production conditions, it is generally under the premise of guaranteeing the production of paint drying rooms that excess heat is re-entered in the iron-drying room (the original burner can be deactivated as the case may be).
2 Making barrels: Under the requirements of environmental protection, the remaining heat recovery can save energy by 5-10%. According to the statistics of a barrel plant, the production energy consumption of the original paint drying room is 950,000 kcal/hour, and the waste heat after installing the environmental protection furnace Recycling for production and use is 750,000 kcal/hour, and it has been used for about three years. It still saves about 5% of energy. It is currently continuing to observe to further improve its product quality.
V. National Environmental Protection Standards:
The allowable emission concentration of triphenyl in the Integrated Air Pollutant Emission Standard GB16297-1996 is:
Pollutants
Maximum allowable emission pollutants (mg/m3)
benzene
12
Toluene
40
Xylene
70
6. Suggestions:
The company is a professional environmental protection equipment manufacturing company. To develop environmental protection business, it is willing to cooperate with drying house manufacturing companies and coating companies to jointly develop new environmentally friendly drying rooms and contribute to the barrel making industry.
Nylon Coated Steel Wire Rope
The fatigue resistance of plastic-coated steel wire ropes is good. For example, the durability of steel wire ropes with nylon coating and nylon core is about 2 times that of ordinary hemp core or metal core (see rope core) steel wire ropes. Plastic-coated steel wire ropes are mainly used in mine hoisting cages, hoisting machinery in meat processing plants, seagoing ship anchors, towing and fishing operations, fishing vessel trawls, etc.
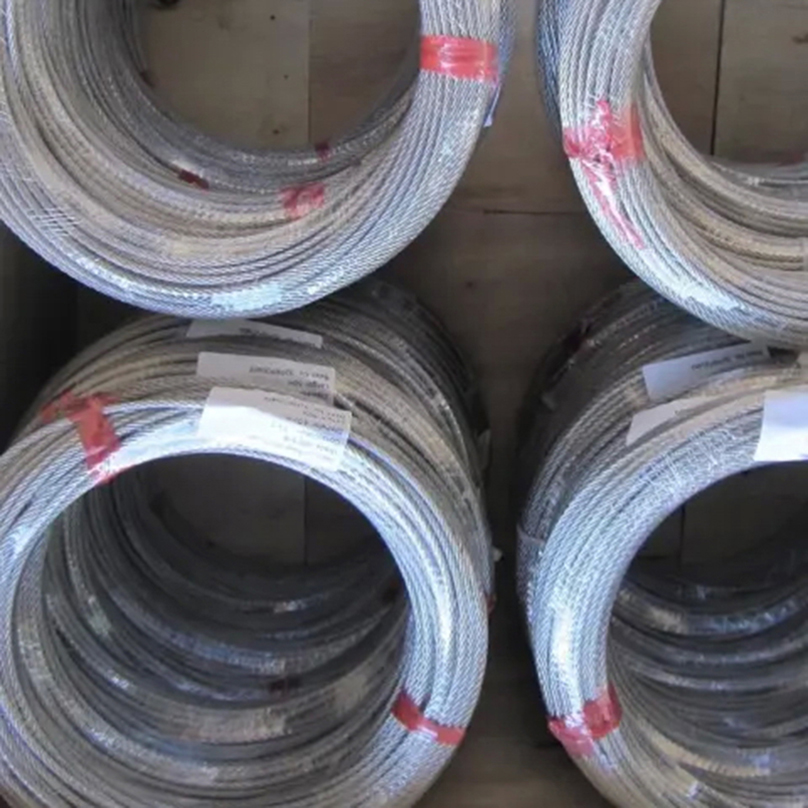
Nylon Coated Wire Rope,Nylon Covered Steel Cable,Nylon Coated Steel Wire Rope,Nylon Coated Stainless Steel Cable
Jiangsu Hongze Stainless Steel Wire Rope Co., Ltd , https://www.hzrope.com